トラックの幌シートで船底カバー製作 DIY
ゴムボで海に出ると心配なのがボートの穴あきです
浮遊物の接触や、海岸での鋭利な突起に接触など様々な原因で穴が開いてしまいます、、
PVC生地のボートは比較的強い生地ですが、私のボートはエコストロンというゴム生地で
擦れや突起に弱いと言われる生地です。
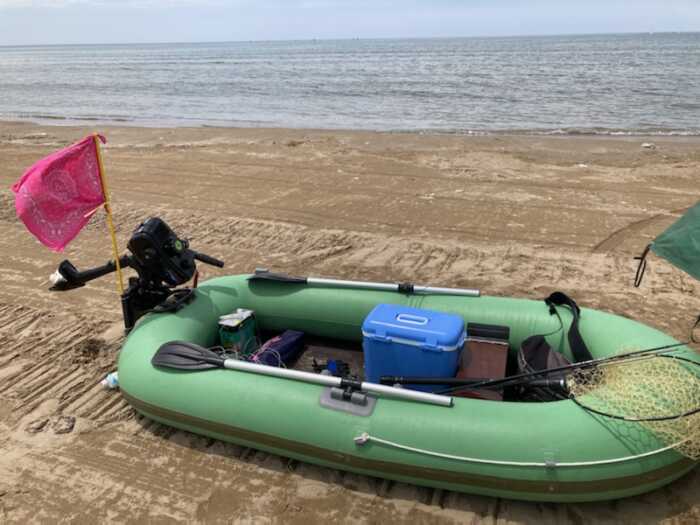
数回、海に出ましたが今の所 穴あきのトラブルは無いですが
そこそこのスピードで走らせると浮遊物を回避できる自身も無く
ゴムボの目線は低いので、そもそも浮遊物を発見しにくい状況です。
私はビビりなので、少しでも安全策が欲しく船底カバーが欲しかったのですが
販売されている物が基本トラックシートで有る事が判明
ならば、工場に捨てようと思っていた軽トラのシート数枚あったので
つなげて船底カバーを作りましょう!
っという事で作っちゃいました。(^^)/
制作手順
1 シート接続
ボートの全長2.6mx1.3m チューブ径0.33m
トラックシート2.7mx2.3mのシートだったので、長手方向をつなげて3.7x2.3mの
長方形に溶着
2 横方向を固定
ゴムボートを膨らませ、トラックシートの中心に置き、横方向2.3mのシートをボートに沿わせ
はと目穴を利用して紐で固定。
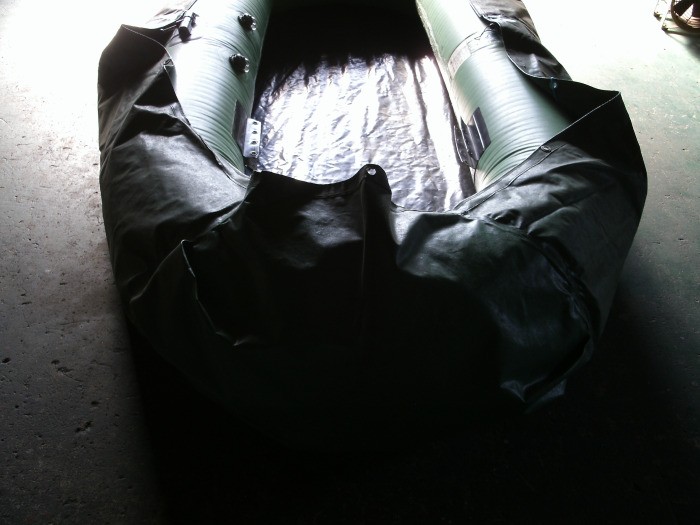
3 船主・船尾部分のカット線入れ・カット
船主船尾の中心部をはと目穴を利用して紐で固定し、シートの角部分を切り取る検討を付ける
マジックで線を入れる。(現物合わせとイメージで)
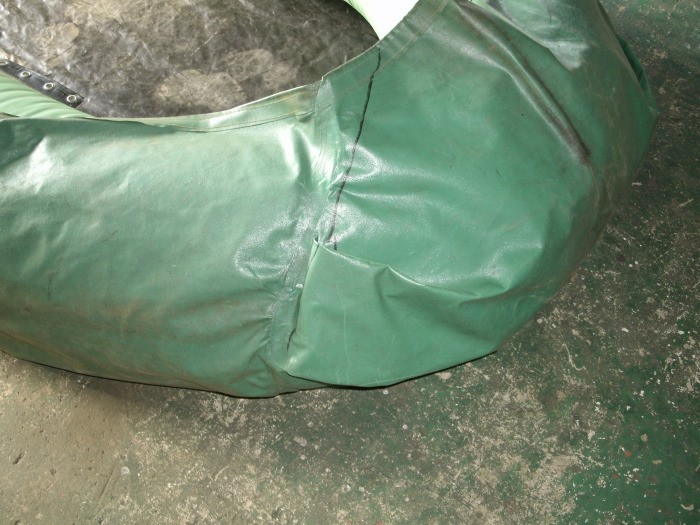
4 オール取り付け部分などの穴あけ
全体のはと目穴に紐を通して、絞り込んだ後、カット位置をマジックで記入しカット。
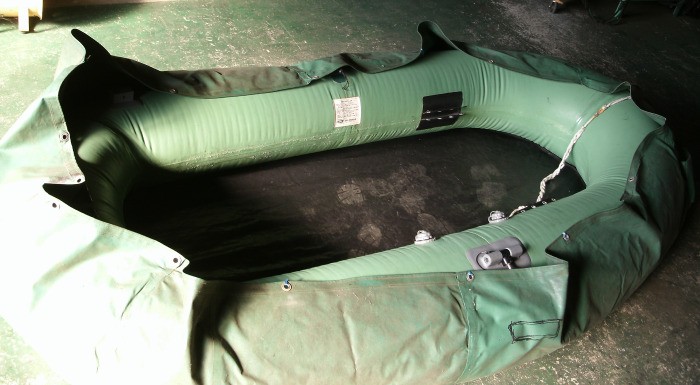
5 完成
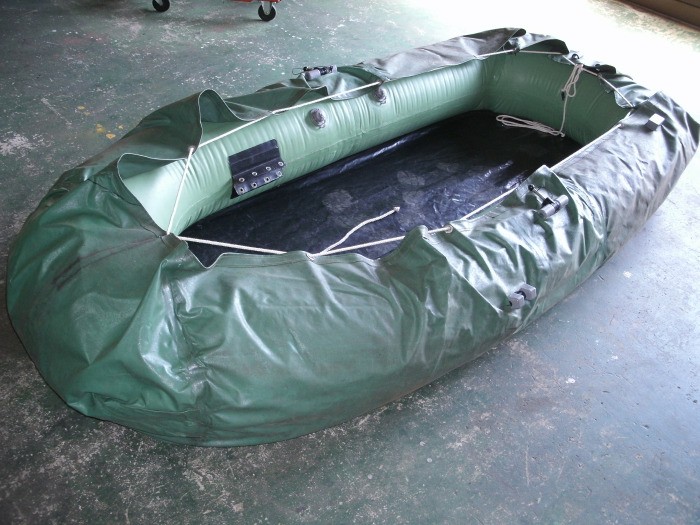
はと目の紐を絞り込むと余りが出ますがDIYなので、、、、
海面の接触部もシワシワで、抵抗がありそうですが とりあえず完成です。(^^♪
今回は、接着剤を使用せず 熱溶着と言う方法でつなげました。
熱溶着とは
熱溶着とは、双方の樹脂自体を溶かし、圧力をかけて二つの樹脂を接着させることです。
この時の樹脂として多いのは、ポリカーボネートやABS、アクリル(PMMA)、塩化ビニルなどです。
熱で溶かして接着する方法に超音波溶着や熱風溶着(溶接)など様々な方法があります。
今回は、熱風溶着でつなげました。
ヒートガンとローラーが必要です。
ヒートガン
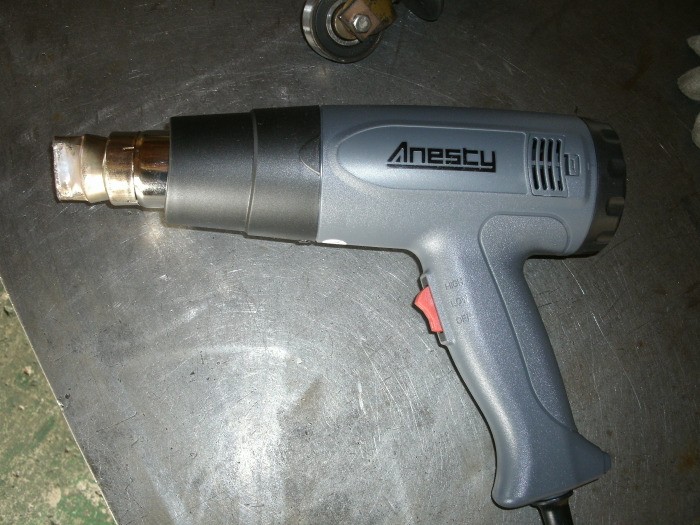
デジタルで温度制御が出来る優れものです(^^)/
ローラー
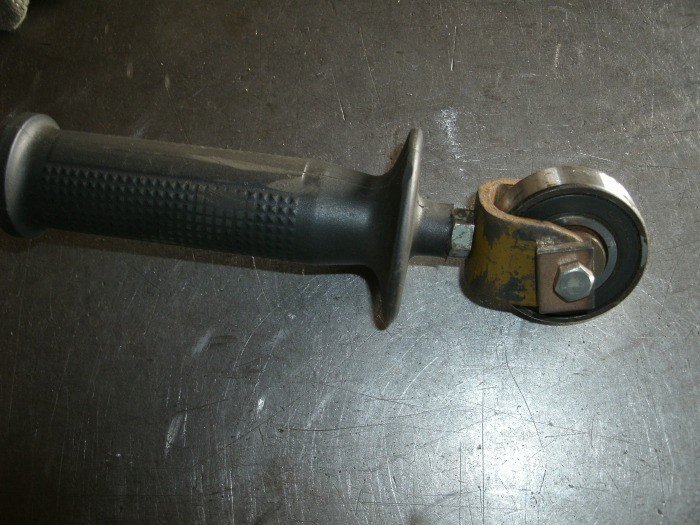
巾15㎜x外径40㎜のベアリングが工具箱に入っていたので、
ジスクグラインダーの柄を取り付けて作ってみました(^^♪
熱溶着の決め手は、ヒートガンで記事を溶かして、直ぐローラーで圧着させることが肝心です。
小難しい工法かと思いきや、意外と簡単です。
ヒートガンで貼り合わせる生地部分を双方溶かし、直ちにローラーで圧着!
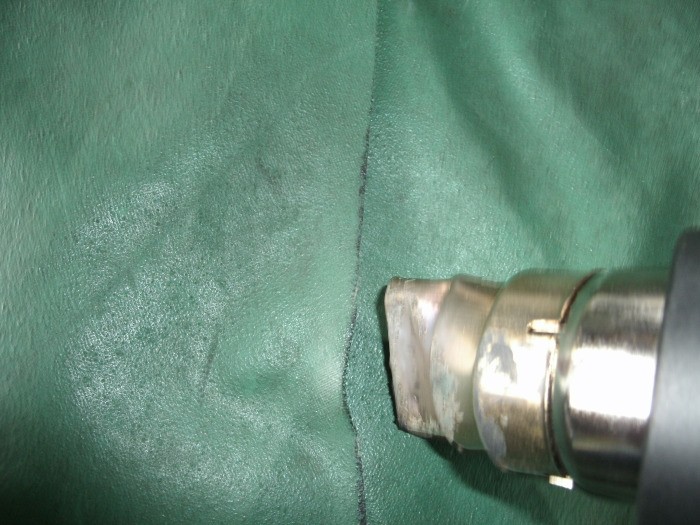
硬化時間も早く扱いやすい工法です。
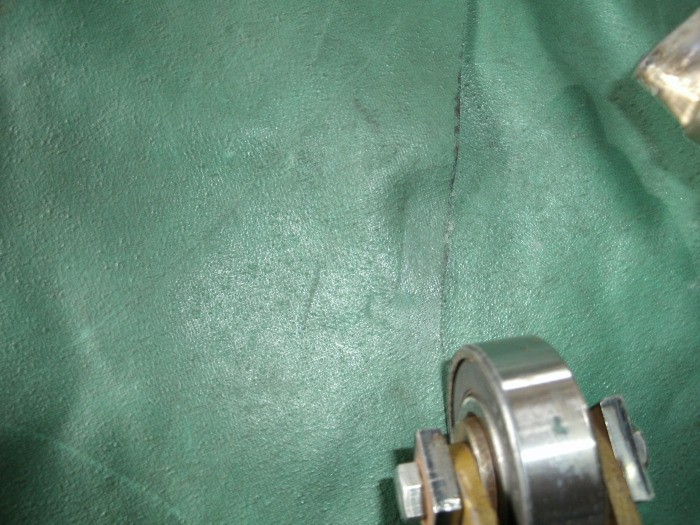
でも、強度は別物
溶着した生地を引っ張っても離れませんが、裂く方向に引くと破れますね~、、、
素人の施工ですので何とも言えません。
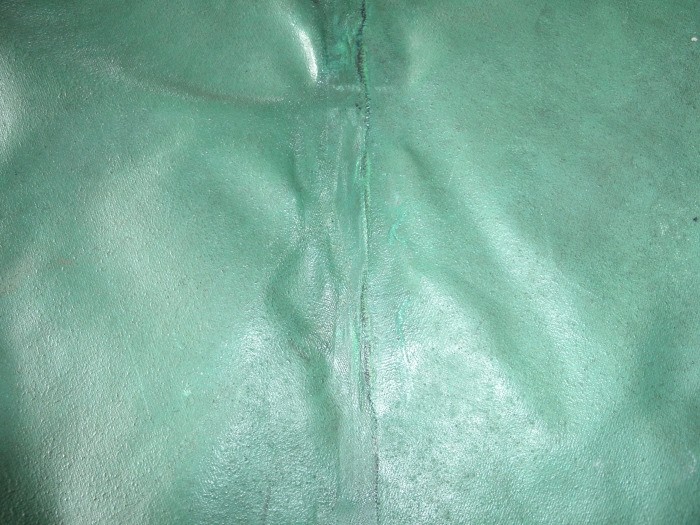
形にはなりましたが 海でバラけることも有るかもしれません(笑)
まあ、カバーなので多少は許容できるでしょう。
まとめ
船底カバーで、溶着したのは2枚接続と船首・船尾の角部分4ヶ所だけなので
DIY品でも行けるのかという感触です。
まだ、海に出てませんが
使用後の感想レポートも追加しますので乞うご期待!
最後までお付き合い下さいましてありがとうございます。
では(^^)/
ディスカッション
コメント一覧
まだ、コメントがありません